在精密制造領(lǐng)域,AB面雙頭開齒機(jī)以其高效、精準(zhǔn)的加工能力,成為齒輪、鏈輪等傳動(dòng)件生產(chǎn)的核心設(shè)備。然而,材料變形與毛刺問題如同“雙生魔咒”,始終困擾著加工環(huán)節(jié)。要破解這一難題,需從設(shè)備設(shè)計(jì)、工藝控制、材料適配三個(gè)維度展開系統(tǒng)性創(chuàng)新。
In the field of precision manufacturing, AB face double head gear hobbing machines have become the core equipment for the production of transmission components such as gears and sprockets due to their efficient and precise machining capabilities. However, material deformation and burrs are like a "twin curse" that always troubles the processing process. To solve this problem, systematic innovation is needed from three dimensions: equipment design, process control, and material adaptation.
設(shè)備設(shè)計(jì)的“抗變形基因”
The 'anti deformation gene' in equipment design
現(xiàn)代AB面雙頭開齒機(jī)正在經(jīng)歷一場“精密化革命”。雙主軸同步技術(shù)通過數(shù)字孿生系統(tǒng)實(shí)現(xiàn)納米級同步誤差補(bǔ)償,將傳統(tǒng)機(jī)械同步的物理誤差轉(zhuǎn)化為算法可修正的虛擬參數(shù)。這種設(shè)計(jì)如同為設(shè)備植入“抗變形基因”,使加工過程中的應(yīng)力分布更均勻,從源頭降低材料變形風(fēng)險(xiǎn)。
The modern AB face double head gear hobbing machine is undergoing a "precision revolution". The dual spindle synchronization technology achieves nanometer level synchronization error compensation through a digital twin system, converting the physical errors of traditional mechanical synchronization into virtual parameters that can be corrected by algorithms. This design is like implanting an "anti deformation gene" into the device, making the stress distribution during the processing more uniform and reducing the risk of material deformation from the source.
刀具系統(tǒng)的革新同樣關(guān)鍵。采用PCD(聚晶金剛石)涂層刀具,其硬度可達(dá)HV8000以上,配合微段差刃口設(shè)計(jì),可將切削力分解為多個(gè)微小矢量,避免局部應(yīng)力集中。更值得關(guān)注的是刀具的“自適應(yīng)浮動(dòng)技術(shù)”,通過液壓緩沖裝置實(shí)時(shí)調(diào)整切削深度,如同為刀具裝上“減震彈簧”,有效吸收加工振動(dòng)。
The innovation of the tool system is equally crucial. Using PCD (Polycrystalline Diamond) coated cutting tools, their hardness can reach HV8000 or above. With the design of micro segment differential cutting edges, the cutting force can be decomposed into multiple small vectors, avoiding local stress concentration. More noteworthy is the "adaptive floating technology" of the cutting tool, which adjusts the cutting depth in real time through a hydraulic buffer device, like installing a "shock-absorbing spring" on the tool, effectively absorbing machining vibrations.
工藝控制的“毛刺防火墻”
The 'Burr Firewall' of Process Control
加工工藝的優(yōu)化需要構(gòu)建“三道防火墻”。首先是預(yù)處理工藝,通過真空熱處理消除材料內(nèi)應(yīng)力,再利用超聲波清洗去除表面微裂紋,為精密加工奠定基礎(chǔ)。其次是參數(shù)優(yōu)化,采用“變參數(shù)切削”策略,根據(jù)材料硬度動(dòng)態(tài)調(diào)整主軸轉(zhuǎn)速與進(jìn)給量,避免傳統(tǒng)恒定參數(shù)加工導(dǎo)致的切削熱累積。
The optimization of processing technology requires the construction of "three firewalls". Firstly, there is the pre-treatment process, which eliminates internal stress in the material through vacuum heat treatment, and then uses ultrasonic cleaning to remove surface microcracks, laying the foundation for precision machining. Next is parameter optimization, using the "variable parameter cutting" strategy to dynamically adjust the spindle speed and feed rate based on the material hardness, avoiding the accumulation of cutting heat caused by traditional constant parameter machining.
更關(guān)鍵的是冷卻系統(tǒng)的升級。傳統(tǒng)乳化液冷卻已進(jìn)化為“氣液雙相冷卻”,通過超臨界二氧化碳與微量潤滑油的混合噴射,在切削區(qū)域形成瞬時(shí)低溫膜,既降低切削溫度,又減少熱變形。這種冷卻方式如同為刀具穿上“隱形冰甲”,將毛刺產(chǎn)生率降低。
More importantly, the upgrade of the cooling system. Traditional emulsion cooling has evolved into "gas-liquid two-phase cooling", which forms an instantaneous low-temperature film in the cutting area through the mixing and spraying of supercritical carbon dioxide and trace lubricating oil, reducing both cutting temperature and thermal deformation. This cooling method is like putting "invisible ice armor" on the cutting tool, reducing the rate of burr generation.
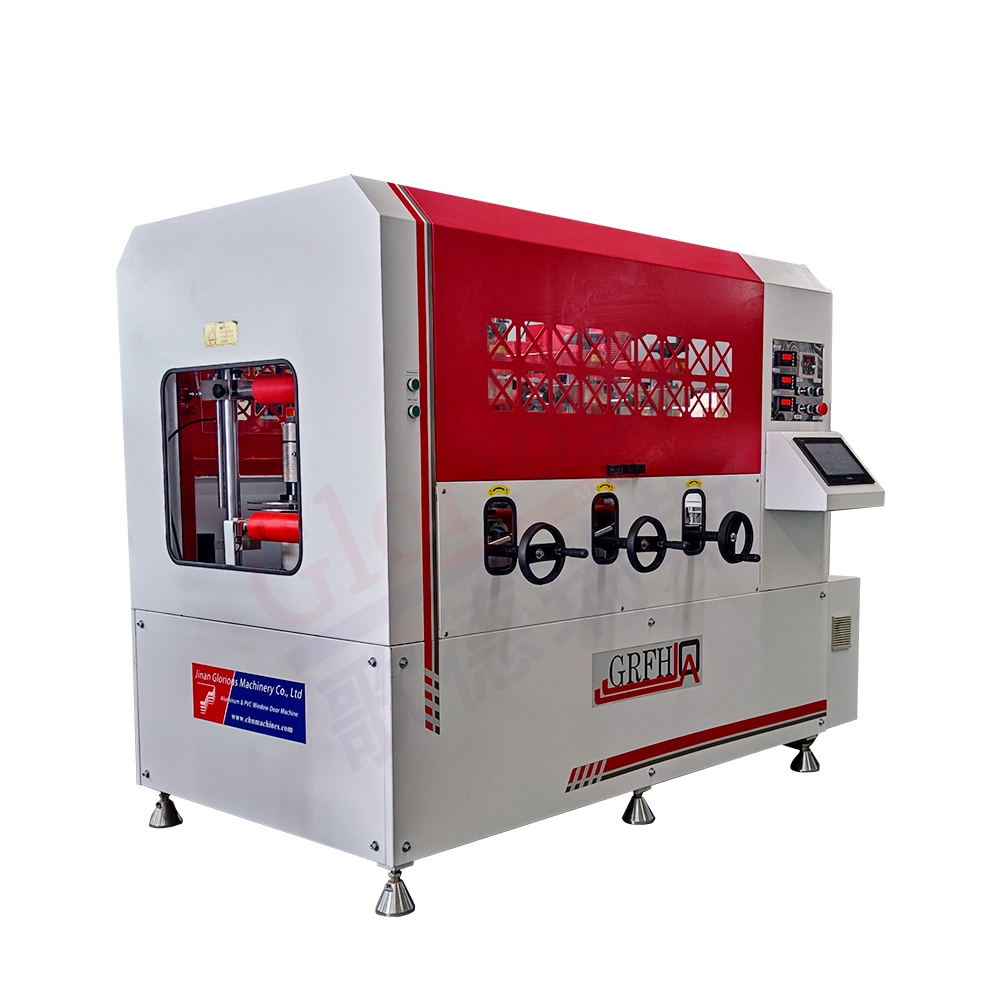
材料適配的“變形補(bǔ)償術(shù)”
Deformation compensation technique for material adaptation
材料特性與加工工藝的適配性,是破解變形難題的“終極密碼”。對于高碳鋼等易變形材料,可采用“預(yù)拉伸-加工-時(shí)效”三段式工藝,通過預(yù)拉伸使材料產(chǎn)生反向變形,加工后的時(shí)效處理釋放殘余應(yīng)力,實(shí)現(xiàn)變形量的相互抵消。
The compatibility between material properties and processing techniques is the ultimate code to solve the problem of deformation. For high carbon steel and other easily deformable materials, a three-stage process of "pre stretching processing aging" can be used. Through pre stretching, the material undergoes reverse deformation, and the aging treatment after processing releases residual stress, achieving mutual cancellation of deformation.
對于鋁合金等軟質(zhì)材料,則需引入“振動(dòng)輔助加工”技術(shù)。通過超聲振動(dòng)裝置使刀具產(chǎn)生微米級振動(dòng),將連續(xù)切削轉(zhuǎn)化為斷續(xù)沖擊,減少材料塑性變形。這種工藝如同為刀具賦予“高頻手術(shù)刀”特性,在保證加工效率的同時(shí),顯著提升表面質(zhì)量。
For soft materials such as aluminum alloys, vibration assisted machining technology needs to be introduced. By using an ultrasonic vibration device to generate micrometer level vibrations in the cutting tool, continuous cutting is converted into intermittent impact, reducing material plastic deformation. This process is like endowing cutting tools with the characteristic of "high-frequency surgical knives", which significantly improves surface quality while ensuring processing efficiency.
質(zhì)量控制的“閉環(huán)管理系統(tǒng)”
A closed-loop management system for quality control
現(xiàn)代AB面雙頭開齒機(jī)已實(shí)現(xiàn)從“開環(huán)加工”到“閉環(huán)管理”的跨越。在線監(jiān)測系統(tǒng)通過多光譜相機(jī)實(shí)時(shí)捕捉加工區(qū)域圖像,利用AI算法識別毛刺萌芽狀態(tài),自動(dòng)調(diào)整加工參數(shù)。這種“視覺-決策-執(zhí)行”的閉環(huán)控制,將毛刺檢測精度提升至微米級。
The modern AB face double head gear hobbing machine has achieved a leap from "open-loop machining" to "closed-loop management". The online monitoring system captures real-time images of the processing area through a multispectral camera, uses AI algorithms to identify the budding state of burrs, and automatically adjusts processing parameters. This closed-loop control of "vision decision execution" improves the accuracy of burr detection to the micrometer level.
更先進(jìn)的設(shè)備還集成“數(shù)字孿生質(zhì)檢”模塊,通過虛擬仿真預(yù)測加工變形趨勢,生成補(bǔ)償代碼反饋至數(shù)控系統(tǒng)。這種“虛實(shí)映射”的質(zhì)量管理方式,使設(shè)備具備自我優(yōu)化的能力,將產(chǎn)品合格率提升至新高度。
More advanced equipment also integrates a "digital twin quality inspection" module, which predicts machining deformation trends through virtual simulation and generates compensation codes for feedback to the CNC system. This "virtual real mapping" quality management method enables equipment to have self optimization capabilities and raises product qualification rates to new heights.
本文由AB面雙頭開齒機(jī)友情奉獻(xiàn).更多有關(guān)的知識請點(diǎn)擊:http://wjfdc.com我們將會對您提出的疑問進(jìn)行詳細(xì)的解答,歡迎您登錄網(wǎng)站留言.
This article is a friendly contribution from the Broken Bridge Aluminum Profile Composite Machine For more information, please click: http://wjfdc.com We will provide detailed answers to your questions. You are welcome to log in to our website and leave a message